Blocking machines’ history
The modern concrete block manufacturing industry is not the result of a gradual evolution but was abruptly driven by the invention of a machine with adjustable removable moulds capable of producing solid blocks.
Solid concrete blocks were first employed in 1832 by the builder William Ranger in England, who patented his version of “Ranger’s Artificial Stone”. Several decades later, in 1860, hollow concrete blocks began to be used for wall construction.
In 1868, a builder named Frear founded what could be considered the first stationary plant to build concrete blocks on the American continent. However, no references to the first block layer were found.
The appearance of the blocks (potser posaria the blocks appearance) that are known today was established when Harmon S. Palmer received its first U. S. patent for “Concrete Block Molding Machinery” in 1887, although there are further patents for other types of machines such as Eichelberger’s in 1905.
Today, concrete blocks are produced virtually all over the world due to their high quality and the demand for economical building materials. A variety of raw materials can be used to produce thousands of concrete units, in different sizes and shapes. The characteristics of the current concrete blocks will be presented afterwards.
The production of blocks also seeks to partially replace a technology that is deeply rooted in our society for the construction of housing that is based on the common brick of fired earth, made with a non-renewable resource and with the effects on the environment that its production brings.
Classification
From the reviewed references it is known that block making machines are manufactured in both developed and developing countries. There are two leading manufacturers of these machines, the People’s Republic of China and the Republic of India.
Following the information consulted, block making machines can be classified as follows:
1. Laying machines
Hydraulics: these are wheeled machines that produce concrete blocks. They place the blocks on a concrete floor and then move to the next position where the new blocks will be placed. This process eliminates the need for wooden or steel platforms. The mold and piston move through hydraulic cylinders, creating a much stronger block and allowing the manufacturer to use less concrete. Any kind of hollow blocks can be manufactured with good quality as well as solid bricks and pavers. An example of these machines is shown in Figure 1.
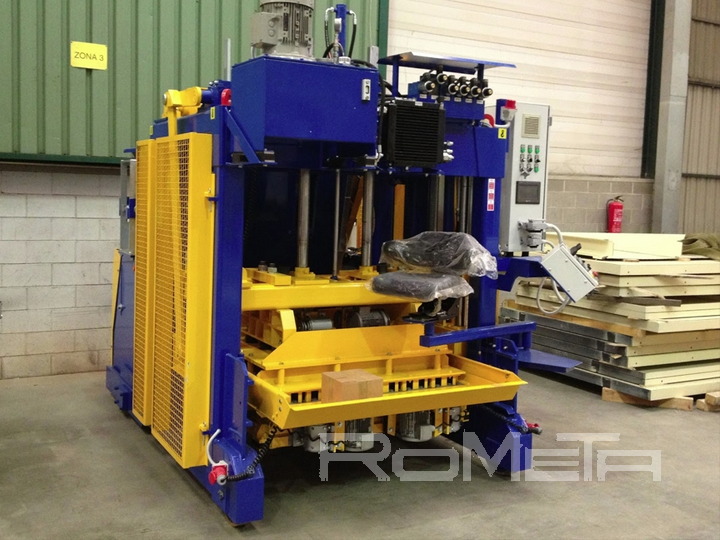
Picture 1 – rometa – hydraulic layerer (https://www.rometa.es/bloques-hormigon-instalaciones/ponedoras-hormigon-instalaciones). Example of hydraulic laying machine
Manuals: these are manually executed machines that produce blocks at low cost. It is perfect for the start-up of small-scale block manufacturing. The blocks are placed on a concrete floor and the machine is moved by the operator to the next laying. This procedure eliminates the need for block handling platforms and manipulators that usually move the green blocks and machine platform before the next blocks can be manufactured. Any type of mould can be mounted on the machine.
2. Stationary machines:
Hydraulics: these are stationary machines that produce concrete blocks. The blocks are placed on a wooden platform and then moved to the floor by the workers. The mould and piston move through hydraulic cylinders. Any type of hollow blocks can be manufactured.
Manuals: these are manual machines that produce blocks at low cost. The blocks are placed on a wooden platform and then transferred to the floor by the operator.
Manual with vibrator of 1 or 2 moulds: they are manual machines that produce blocks of 1 or 2 moulds. The vibrator improves the quality of the blocks. The blocks are placed on a wooden platform and then transferred to the floor by the operator.
3. Automatic Stationary Plants:
These machines they have batch processing, automated concrete mixing and pressing systems. The transfer of the blocks is carried out by a transfer system, usually through conveyors. The productivity of these machines, depending on the block type, can range from 12.000 to 20.000 blocks in 8 hours. Human effort is minimal. These are the most expensive machines.
The following describes the main advantages and disadvantages of Laying and Stationary machines, excluding plants:
Laying machines:
Advantages:
- No platforms are required for the transfer of the produced blocks.
Disadvantages:
- A fairly large concrete slab is required for production. The slab is expensive and its dimensions must be according to the production.
Stationary machines:
Advantages:
- A relatively small space is required for production.
Disadvantages:
- Platforms are needed to move the blocks produced. These platforms are initially expensive and need to be replaced when damaged in daily work.
You may see more block machines and types in the Rometa block factory, from where we got the information.